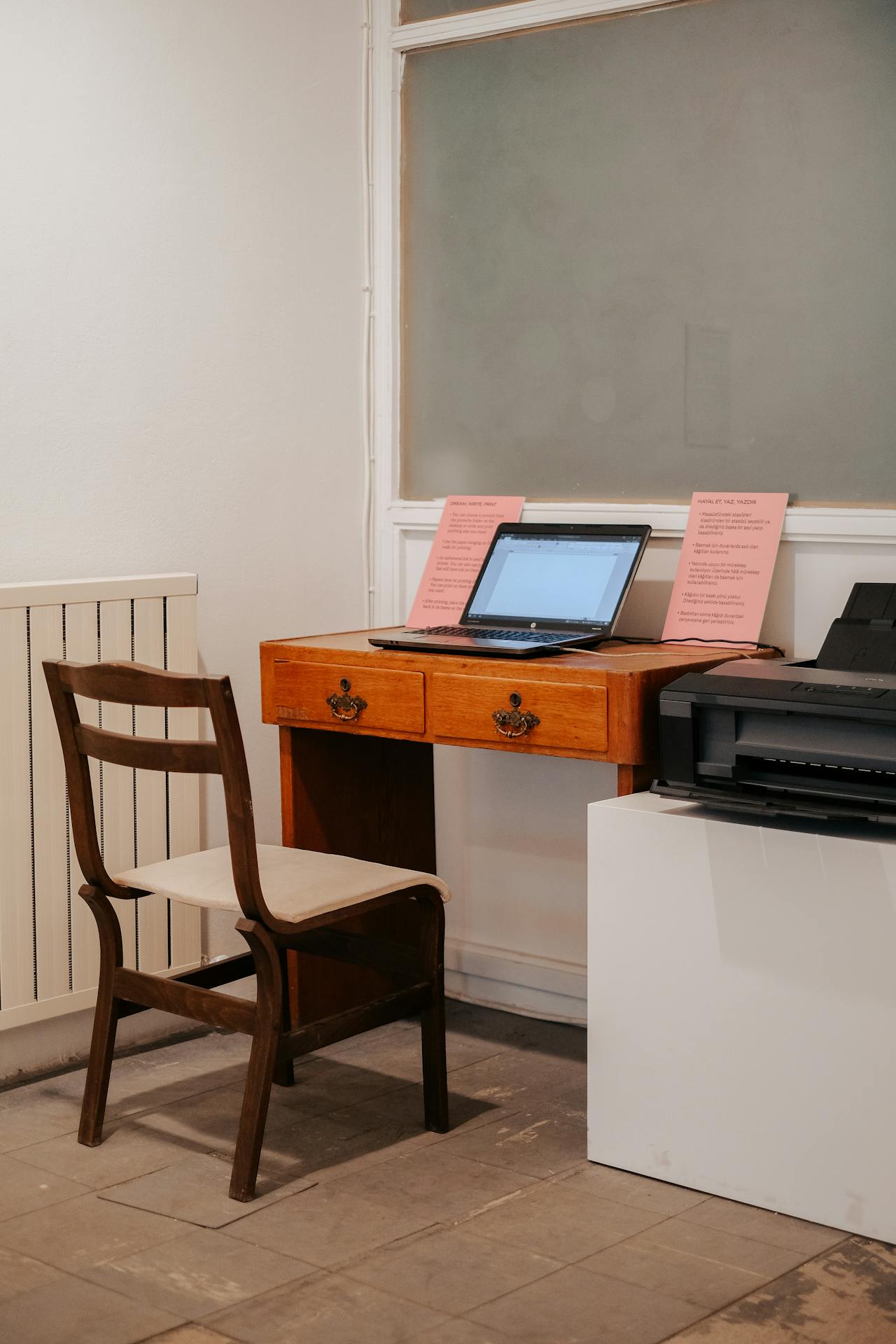
Key Takeaways
- 5 Preventive Steps to Ensure Line-Free Copies after Every Service Visit. This means no more line-free copies after each service visit.
- Step 4: Conduct thorough inspections of each key copier part. Calibrate them per the manufacturer’s specs to reduce the likelihood of unexpected failures and guarantee effective performance.
- Choosing nothing but premium, proven supplies keeps your valuable equipment safe. It delivers superior print quality, too, by using paper that’s been approved for use and using genuine toner or ink.
- Create technical and administrative service visit checklists. This step helps make sure all corrective actions taken during maintenance are done accurately, avoiding mistakes that cause copy defects.
- Educate end-users on how to identify early warning signs that indicate potential copy quality problems. Engage and empower them to report issues, and you’ll fix small problems before they become major catastrophes.
- Taking a preventive maintenance approach will maximize your equipment’s lifespan. Not only is it more economical by reducing downtime, but it also helps defend your professional reputation.
Preventive steps 1 through 5: You want easy tests that provide straightforward answers. By routinely cleaning glass, rollers, and other scanner components, you can prevent dust from creating line-like marks on copies. Routine toner and drum unit inspections prevent lines from appearing on your copies. Replacing worn-out wiper blades and feed rollers ensures a line-free, continuous feed. Test page run: Running a test page catches errors immediately. Just use the right paper. Nearly half of all service calls are for paper jams or streaks. Here are the five preventive steps that ensure line-free copies after every service visit. These five preventive steps can be followed on virtually all copier models. In the main part below, you will see why each step matters and get tips for easy upkeep in your daily work.
Why Lines Appear
There’s nothing more irritating than seeing ugly lines or streaks on every copy. These lines are not arbitrary; they originate from personal, practical, and behavioral faults in the way you use, wash, and maintain your device. Implementing a preventive maintenance strategy is crucial to producing line-free copies after every service. Understanding how to identify these issues is vital for effective preventive maintenance.
Post-Service Causes
Dirty areas remaining post-service visit are the number one reason for lines. Residues or dust on the glass, rollers, or drum will appear as streaks on your copies. Even a minor blemish can result in an ugly streak running down every page. If a tech doesn’t catch this during their cleaning, you’ll notice it on your next set of prints. To mitigate these issues, implementing a preventive maintenance program can significantly enhance print quality by ensuring regular inspections and adherence to manufacturer guidelines.
Technician errors and omissions contribute to these problems. If important maintenance tasks, such as aligning the drum or replacing worn rollers, are not performed promptly, your print quality suffers. A proactive approach to maintenance scheduling can help avoid such oversights. By ensuring every change is inspected before the vehicle is returned to service, you can prevent the majority of line problems and extend the equipment’s lifespan.
Spotting Trouble
Staff should know the first sign of trouble: faint lines, odd marks, or faded zones on prints. With early warning, you’ll be able to take action quickly, before damage escalates.
You want continuous monitoring, all the time, not just when it’s brought in for repair. Pay attention to grinding, squeaking, or any strange noise. These frequently indicate a roller that is misaligned. If you notice any lines or defects, log them immediately. So don’t wait. Even if you don’t conduct a full audit, it’s worth documenting every defect, whether notes or photos, so you can detect patterns over time.
Routine tracking of print counters, toner levels, and unit cycles is effective. Keep an eye on these figures! You will be aware when a component is approaching the end of its life, so you can plan for replacement service before any queues develop.
The True Cost
It’s common sense — preventive maintenance is less expensive than reactive repair. See the cost comparison:
Type |
Cost per visit |
Downtime (hours) |
Avgannual cost |
Preventive |
$70 |
0.5 |
$350 |
Reactive |
$180 |
4 |
$900 |
It’s no surprise, then, that unplanned repairs damage productivity. Downtime doesn’t just make work take longer—it costs you work, deadlines missed, undue stress to your team, and more. Wise investment in regular maintenance prevents major deterioration of your system, reduces the chance of unexpected failures, and protects you from higher repair costs down the line.
Five Steps: Flawless Copies
Consistent, bowing-free copies are a direct reflection of how well your equipment is maintained and the degree to which your team cares about the details. Implementing a preventive maintenance strategy allows you to be proactive, taking action before problems begin. These five steps outline a systematic maintenance process, ensuring that preventive maintenance activities lead to flawless copies becoming the expected result.
1. Full Component Audit
Full Component Audit: Begin with an audit checklist. Every critical part matters: rollers, imaging units, fusers, and feed trays. Even minor wear can appear as streaks or lines.
Plan audits at regular intervals—once a month or after each service appointment are possible options for a preventive maintenance strategy. This proactive approach cuts the chances of unexpected failures and allows you to better forecast your needs. Every inspection should be recorded, providing a clear picture of the condition of each component. In the long term, these written accounts serve to identify trends. If you notice that one specific area is consistently wearing down, you can modify preventive maintenance schedules and/or funding to repair it before it becomes a pattern. This meticulous documentation enables more informed choices.
2. Exact Calibration
Exact calibration. For flawless copies, exact calibration is critical. As always, make sure to consult the specifications from your manufacturer for proper alignment and setup. Calibration tools and built-in software have made this much easier—use them to regularly check and make adjustments if necessary.
Misaligned measuring components may lead to feed errors or defects in the output copy. Get into the routine of inspecting these at the end of any service. Educate staff to ensure that everyone understands how and why correct calibration is important. Similar to preserving evidence in forensics, calibration ensures the integrity of flawless copy production.
3. Post-Service Cleanse
Post-Service Cleanse: Cleaning immediately following service is essential. Dust, toner, and other debris are major contributors to print defects. Use appropriate cleaning tools—soft brushes and lint-free cloths—so you avoid damaging sensitive components.
On-site follow-up is crucial; scheduling a brief inspection after the clean helps ensure everything is in order. This process, similar to a preventive maintenance strategy, prevents minor errors from escalating into major complications. Ensure all your techs fully understand the cleaning procedure before leaving the job site.
4. Use Quality Supplies
Avoid shorting yourself on paper or toner. Simply use paper that meets copier specifications and steer clear of low-quality suppliers. Always use authentic toner and ink, as low-cost knockoffs can lead to paper jams or other issues that only show up down the line.
Monitor stock on supplies regularly. Develop relationships with reliable suppliers to maintain quality and prevent a panic scramble.
5. Verify Performance
Establish high standards for copy—darkness, clarity, and no ridges. Perform post-service test copies and check against previous results. Monitor performance to catch trends before they develop.
Solicit user feedback on print quality. In my experience, their input can truly uncover glaring problems that you might overlook.
Optimizing Service Visits
To achieve line-free copies after every service, a preventive maintenance strategy is essential, extending beyond just the basics. Preventive measures must align with the usage level of your equipment. Collaborate with your service team to pinpoint the biggest opportunities for improvement. Ensuring that all necessary tools and parts are available before the visit is vital! Reviewing service records beforehand helps identify trends or recurring issues, which ultimately reduces the risk of failures and saves costs by preventing issues from escalating.
Technician Skill
Having highly skilled technicians is important. When you go to hire, choose candidates who have practical experience repairing the same kind of machines. They need to be continuous learners. Providing them training on the new fixes keeps your team sharp.
Provide opportunities for your techs to discuss their experiences in the field. By sharing their stories, they enable others to learn from them and identify trends early. Review their work regularly—it’s just good business! Consider their first-time fix rates and error rates. This ensures that you’re maintaining the high bar that you’ve set.
Standard Protocols
Standard Protocols: Establish a uniform, easy-to-follow checklist for each service visit. Write your protocols so a layperson can see them, someone who doesn’t know anything about the process. This ensures a high-quality service visit experience is consistent throughout your entire organization.
Prioritize safety, starting with the service visit and all the way to deployment, rather than treating it like an add-on. Standardize protocols. As technology evolves, have every guide readily available and ensure your team stays ahead of the curve. Well-kept records make training new personnel much easier and keep the whole team moving in the same direction.
Sidestep Errors
Employ checklists for each visit. Most importantly, they assist techs in identifying critical steps in a process that they may overlook. A mindset of checking everything before an employee leaves prevents minor mistakes from turning into major ones.
Tech tools are better equipped to catch other obvious misses. For instance, electronic maintenance logs can identify components that wear out quicker than expected, using asset failure history data. When your line crew feels comfortable discussing errors, you can address underlying issues, rather than treating just the symptoms.
Sustaining Copy Quality
Line-free copies per service visit require establishing good habits and systems that help you maintain your copier long-term. Implementing a preventive maintenance strategy through five clear steps—empowering users, controlling the environment, sticking to preventive maintenance schedules, supporting ongoing learning, and driving accountability—works together to keep standards high and issues rare.
User Empowerment
You don’t just need the functional machine; your users must understand how to use it correctly. These training sessions occur when a new person comes on board or every six months, focusing on a preventive maintenance strategy that empowers users to identify issues proactively and address basic repairs. Clear guides, complete with pictures and simple steps, help your team clean feed rollers, clear jams, or check toner levels without waiting for IT. With an easy online form or chat channel, anyone can flag a missed streak or paper jam, ensuring nothing gets past. Gamify it—give the crew incentives for fast reporting or clever repairs! Whether it’s a shout-out or a small perk, it goes a long way and fosters a sense of ownership during the assembly.
Control Environment
Excess dirt, airborne contaminants, heat, or UV light can damage internal components and lead to premature copier failure and streaky prints. It’s important to place the copier in an area with consistent air circulation and free from drafts from windows or space heaters. Inspect the space periodically to see if there is a buildup of dust or obstructed air returns. Basic temperature and humidity meters are useful for monitoring the range of comfortable (<25°C) and humid (40–60%) conditions to maintain a stable home. If you start to see warping, jamming, or lines, it could be the environment that’s causing the issue. Just relocating the copier or bringing in a fan could make big changes!
Quarterly audits are a good idea. They reel in holes in your printer’s environmental health, and your efforts are paying off.
Routine Care
- Assign daily cleaning to one person
- Weekly check for toner by another
- Monthly inspection of rollers by a third team member
- Review the logbook once per month
Establish preventive maintenance schedules using calendar reminders or a shared app to cue each step in your maintenance strategy. Keeping a record of completed work and dates simplifies identifying missed steps or emerging trends in your preventive maintenance efforts.
Ongoing Learning
Brief refresher courses keep your team’s skills fresh and support a preventive maintenance strategy that avoids sloppy or unsafe work. Open huddles to all—short meetings where you discuss what’s going well, what needs to change, and how to address it. A straightforward tracking sheet, reviewed by a supervisor, allows you to identify when and where good habits fall through and address them. Senior leaders must provide explicit direction, modeling how minor measures lead to the accumulation of bigger issues.
The Value Of Prevention
Prevention is the key to keeping your copier fleet dependable and your business up and running. By implementing a preventive maintenance strategy, you can ensure that every visit is an opportunity for preventive maintenance activities. This not only makes your devices more useful for longer but also contributes to a more productive workplace. Such preventive maintenance efforts yield tangible, quantifiable value across various sectors, from local tech small businesses to multinational health powerhouses.
- Reduces the risk of sudden breakdowns, ensuring steady operation.
- Reduces the cost of repair and replacement of parts by minimizing wear.
- Extends the time between necessary device upgrades.
- Preserves output quality, which reflects on your business reputation.
- Protects worker health and safety. Supports compliance with workplace safety standards, including mitigating risks associated with equipment failure.
The readability of your copies reflects your business’s credibility. Dirt, smudges, or streaks suggest a lack of care, potentially damaging your credibility in the eyes of customers or collaborators. Prioritizing clear printouts sends a message that you care about quality and details. High-quality, well-maintained copiers help you avoid costly repairs and workflow interruptions, enabling your team to focus on what truly matters.
Save Money
- Plan to perform preventive maintenance on a set schedule—every three or six months—to prevent premature breakdown that can be expensive to fix.
- Compare the long-term ROI: maintenance programs often cost less than repeated emergency repairs and unplanned downtime.
- It’s been proven that reactive maintenance costs up to three times as much in five years.
- Preventive budgeting is the idea that you can budget for small, expected costs rather than large, unpredictable ones.
Extend Life
When you maintain your copier on a preventative service plan, you reduce wear and tear. Choose quality components, such as OEM toner and OEM rollers, so each part works longer. Hospitals have applied this same concept, investing in preventive care such as screenings and annual check-ups to identify and address issues before they require more expensive treatments.
Success stories from the tech and healthcare sectors show this is possible. In one instance, the average copier life has been increased by two years through routine cleaning and calibration in clinics. Keep in mind that every dollar spent on maintenance isn’t a dollar lost—it’s money saved.
Ensure Clarity
Legible reproductions ensure clear, professional business communications. An out-of-focus or washed-out presentation may mislead customers or associates, damaging your brand.
Every customer touchpoint, from invoices to sales presentations, relies on sharp prints. When copy quality decreases, your brand just looks sloppy. Consistent quality assurance means you uphold the best quality consistently and never again fear what shape your work will take.
Boost Output
Fewer jams mean more work done.
Teams move at a quicker pace when provided with tools that don’t fail.
Downtime drops, output jumps.
Regular maintenance increases output by as much as 20%, based on industry statistics.
Your Expert Partner
Your reliable expert partner goes beyond just managing your machines; they implement a preventive maintenance strategy to ensure your copiers are operating at peak performance. With practical expertise and keen insights into analysis, you receive an expert partner for each stage of maintenance. Our dedicated team provides straightforward strategies and transparent communication, keeping you informed about preventive maintenance programs and tangible assistance every step of the way.
Deep Analysis
Our highly trained experts implement a preventive maintenance program to analyze each copier with a fine-tooth comb. We test all aspects of the print quality, paper travel path, and hardware components. Using super accurate data collected from your device, including page counts and previous error logs, we can identify issues before they occur. This proactive approach allows us to detect very faint lines or streaks early on. Each time you visit, you will receive a complete diagnostic report detailing the condition of your copier and documentation on any damaged or aged components. We walk through each finding with you, ensuring you’re informed and can take preventive actions to avoid issues in the future.
Custom Plans
Each copier, like any other piece of equipment, comes with a varying workload. Some print constantly, every day, while others print only a handful of pages a day. We partner with you to create a customized preventive maintenance program that matches your copier’s actual usage. This smart plan expands as you do, ensuring that preventive maintenance activities are aligned with your evolving needs. You receive exclusive content detailing the work we’re doing, why it’s important, and how this all contributes to putting an end to orange lines on your prints. We help you clearly understand how all these measures save you money and aggravation from day one.
Lasting Support
We’re your expert partner every step of the way, especially when it comes to implementing a preventive maintenance strategy. When an issue arises—not if—you have playbooks and a dedicated human being at the other end of the line. Our support line is fast and direct, ensuring your equipment is serviced to maintain optimal condition and establish reliability and trust. After every project, clients tell us that our assistance is not only prompt but refreshingly straightforward, reinforcing our commitment to proactive problem management.
Conclusion
A strong, line-copy-free quality begins with consistent, preventive measures. Clean the windshield – inside and out. Step 2—Clean the rollers regularly. Step #2 — Check the toner. Image by John McCafferty. Check the brake drum. As an additional precaution, run a test print. Each job joins the fight individually to eliminate lines at the source. You produce crisp copies that cut down on service time and demonstrate your expertise. Basic measures such as these ensure your machines are operating at peak performance. You serve your team when you ensure success. Not only that, you’re saving dollars and reducing anxiety. By making these habits part of your workflow, you can ensure your work remains line-free and your service visits are hassle-free. You raise the standard for your industry colleagues and earn trust with your customers. Make sure these steps are part of your maintenance checklist. Follow our blog for more tips and tricks! Engage with practitioners who are just as committed to getting it right as you are and pass along your advice.
Frequently Asked Questions
1. What Causes Lines To Appear On Copies?
Lines on copies often arise from dust, toner build-up, or scratches on the scanner glass and internal components. Implementing a preventive maintenance strategy, including regular cleaning and proactive maintenance activities, can effectively avoid these issues.
2. How Can I Prevent Lines After A Service Visit?
Ensure service technicians implement a preventive maintenance strategy by properly cleaning the scanner glass and changing worn parts with every visit. They also need to calibrate toner quality, align the drum, and update software to enhance equipment life!
3. Why Is Cleaning The Scanner Glass Important?
Regular inspections of the scanner glass will help maintain its efficiency and prevent unplanned downtime. By keeping it free of dust and fingerprints, you ensure clear, readable copies every time.
4. How Often Should Internal Parts Be Checked?
Regular inspections of internal parts are crucial, as worn or damaged components can lead to costly repairs and unplanned downtime, ultimately affecting overall copy quality.
5. Can Outdated Software Cause Copy Defects?
Can obsolete software impact copy quality? Implementing a preventive maintenance strategy requires performing and documenting a full firmware and driver update at every maintenance appointment.
6. What Are The Long-Term Benefits Of Regular Preventive Steps?
Regular preventive maintenance strategies lead to less unplanned downtime, lower overall repair costs, and line-free copies, which enhance productivity, user satisfaction, and the bottom line.
7. What Should I Expect From A Professional Service Provider?
Expect copy cleaning, wear and tear inspection, and preventive maintenance activities, along with software optimization and expert tips to keep line-free copies coming after every service call.
Transform Your Office With The Best High-Volume Copiers In Concord, California!
Are you searching for a reliable high-volume copier near Concord, California? Look no further! At Office Machine Specialists, we’ve been the go-to experts in servicing and selling top-notch office equipment since 1995. As a trusted family-run business, we’re committed to providing you with the best equipment options and exceptional after-sales service.
With decades of experience, choosing the right high-volume copier can be overwhelming. That’s where we come in. Our knowledgeable team will ask the right questions, understand your unique requirements, and guide you toward making smart decisions for your business. Whether you’re looking for a new machine lease or a purchase, we’ve got you covered.
We’ve witnessed the evolution of copiers from the pre-Internet era to the cutting-edge digital workflow environment. Our expertise spans efficient high-volume printing, seamless scanning, advanced account control, and fleet management. Our extensive experience with all the major brands makes us an invaluable resource your organization needs.
Don’t settle for anything less than the best. Contact Office Machine Specialists today for all your high-volume copier needs. Let us help you streamline your office operations and increase your productivity!