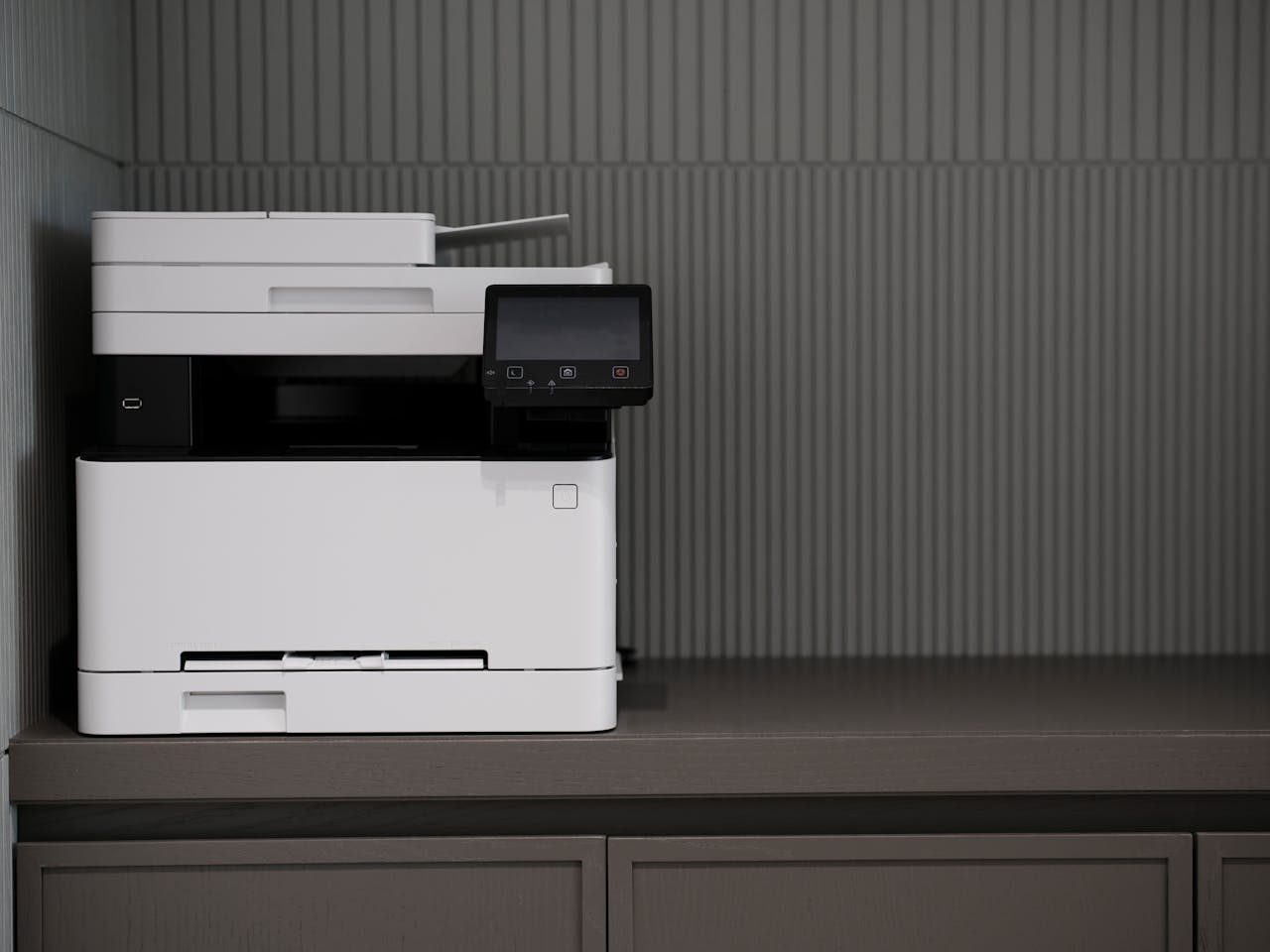
Key Takeaways
- Preventive maintenance is the key that will ensure your copiers continue to be in peak condition and working for you. It means routine cleaning, inspection, and maintenance. This proactive approach saves companies thousands in repairs and maintains operational efficiency.
- Preventive maintenance investments lower repair costs by 33 percent, according to the American Public Works Association, as small problems are addressed before they become major failures. It’s the smart, cost-effective approach that spares businesses from spending thousands of dollars on surprise repairs.
- Preventive maintenance reduces downtime Preventive maintenance means that you spend less time waiting on copiers to be serviced. Regular maintenance stops sudden breakdowns from disrupting critical workflows, improving employee efficiency and the bottom line.
- Preventive maintenance helps avoid performance issues and non-functioning copiers by keeping print quality, speed, and overall operation in top shape. For businesses, that means fewer headaches from faulty equipment and steadier output.
- Preventive maintenance increases the lifespan of copier machines, which saves businesses money in the long run. Because they are a major investment, proper care can maximize return on that investment by delaying the need for costly replacements.
- By preventing everyday annoyances such as paper jams, print quality issues, or software malfunctions, regular maintenance helps keep your office copiers functioning at optimum performance. By making these preventive measures a priority, businesses can reduce unwelcome disruptions while ensuring their company is operating at maximum efficiency.
Preventive copier maintenance can save your business thousands in repair costs and downtime. Routine service ensures that your copier is always in top working order, avoiding easy-to-spot problems such as paper jams, streaky prints, or mechanical malfunctions.
Basic maintenance procedures like cleaning parts and inspecting for damage or wear can go a long way in prolonging your equipment’s life. By catching issues before they become serious concerns, you save thousands in unexpected repair costs and keep your business productive.
Regular maintenance keeps machines running more efficiently, which saves on energy costs in the long run. By investing in consistent, routine care, you can get the best performance while safeguarding your budget from costly surprise repairs.
With little effort, preventive maintenance offers long-term savings and peace of mind that your office operations are running reliably.
What Is Preventive Copier Maintenance
Preventive copier maintenance is a proactive approach aimed at keeping copiers in optimal working order. This approach gets ahead of problems and makes preventive measures. It consists of routine inspection, maintenance, and correction to ensure that devices perform optimally.
By preventing potential problems before they worsen, businesses don’t have to bear the expensive burden that sudden repairs or replacements would cost. Reliable maintenance expedites the copier’s performance. It increases the lifespan of your printers, so you won’t find yourself investing in new equipment as frequently.
Preventive maintenance goes a step further by being proactive with the equipment. Regular maintenance equals regular attention. Reactive maintenance only comes into play once a failure has already occurred.
The savings are astounding—those companies that engage in preventive maintenance can save $4 to $9 for every $1 they spend maintaining their infrastructure. In fact, a well-structured program can reduce unplanned downtime by over 50%.
As a result, there are fewer interruptions and it improves overall workflow productivity. This proactive approach prevents breakdowns, improves overall reliability, and keeps your business running without interruptions.
Why Preventive Maintenance Is Important
Preventive maintenance is often the key to keeping copiers running smoothly and aligning with business goals. It saves you from expensive repairs, saves you from operational downtime, and increases the equipment’s longevity. By catching potential problems on the front end, businesses can trust that their machines produce top-of-the-line work. This proactive approach saves them from the financial strain of unexpected breakdowns.
Read below to find out how preventive maintenance can help you save time and money and improve efficiency.
Reduces Repair Costs
Preventive maintenance allows us to discover and fix small issues before they become big problems. For example, cleaning internal pneumatic components or replacing other worn parts and components prevent potential mechanical failures, saving businesses thousands of dollars in repair costs.
Research indicates that preventive maintenance is at least 25–30% less expensive than other maintenance strategies, which makes it a fiscally responsible strategy. Preventive maintenance will not only lower the amount of costly repairs required but provide tangible savings as well.
In turn, businesses should view this as a wise investment. It ensures long-term fiscal returns instead of looking at it as an external cost.
Minimizes Downtime
Given that copiers can be expensive, scheduled maintenance means they are less likely to suddenly stop working. Downtime can paralyze workflows, risking a loss in productivity and the potential for missed deadlines.
Industries experience annual losses of $20 billion to $60 billion from the effects of unscheduled downtime. Preventive maintenance allows departments to run more efficiently and effectively so employees can carry on with their work without interruption.
For instance, with timely service, your machines are always running their best during the most demanding times, maintaining efficiency and preventing you from falling behind the competition.
Improves Copier Performance
Routine maintenance helps maintain the highest quality of print by ensuring that important components are operating at an optimal level. Cleaning printheads, calibrating sensors, and replacing consumables help prevent problems that affect output quality.
This reliability fosters customer trust, an invaluable asset in today’s market. Preventive maintenance tricks toner into working more efficiently, minimizes errors and ensures that businesses are producing professional quality work.
By making these practices a priority, copiers are sure to operate at peak performance, helping businesses maintain smooth daily operations.
Increases Equipment Lifespan
Regular upkeep, repairs, and diagnostics that come with preventive maintenance directly affect the longevity of copier machines by preventing wear and tear. Poorly maintained equipment is much more susceptible to unexpected breakdowns that lead to expensive new purchases.
Preventive care safeguards your ROI, helping machines run like new for years to come. Organizations that implement such strategies are able to lower downtime by as much as 85%, reaping the highest returns.
In one instance, regular inspections and replacement of worn parts was proven to extend the life of high-volume copiers, reducing lifecycle costs significantly.
Common Copier Issues Prevented By Maintenance
Proper maintenance is key to keeping copiers reliable and cost-efficient. It fixes small problems before they develop into expensive breakdowns, keeping your business running uninterrupted and increasing your company’s overall efficiency.
Read on as we discuss frequent copier issues and how preventive maintenance can prevent them.
Paper Jams And Misfeeds
Paper jams are commonly caused by paper dust, improper loading, or rollers that need replacing. Cleaning internal components and paper trays removes debris accumulation, and feeding problems caused by the wrong paper can be avoided by using high-quality paper.
Misfeeds can be prevented by ensuring that paper stacks placed in trays are properly aligned, too. For instance, maintaining roller traction prevents paper jams due to slippage.
Maintaining a room humidity level of 40-60% will help minimize static cling, one of the most common causes of jams.
Poor Print Quality
Dirty internal components and the incorrect use of ink can lead to print quality issues. Prevent smudging from correction fluid residue by cleaning regularly per the copy machine maintenance schedule, particularly copier glass.
Using high-quality toner and ink helps maintain clear text and image quality, and regular printing of test pages keeps OEM ink from drying out. Routine inspections keep all output uniform, eliminating costly reprints and waste.
Overheating Or Power Failures
Overheating occurs from blocked vents or lack of airflow. Maintenance removes dirt and dust from vents and prevents overheating.
For example, installing copiers in areas with good air circulation prevents overheating. Maintaining the electric power supply routine checks of power supply components reduce unexpected failures, keeping your operation safe and extending the copier’s life.
Software And Connectivity Problems
When the firmware is outdated or there are software issues, connectivity is interrupted. Regular software updates keep your copier compatible and secure.
Regular maintenance catches network problems before they escalate, ensuring that all printing needs are met without interruption. Keeping your firmware up to date helps your devices run smoothly and shields them from emerging threats.
Types Of Preventive Copier Maintenance
Preventive copier maintenance is essential for prolonging machine life and preventing major repairs, ensuring consistent equipment functioning at peak performance. Many copier providers emphasize the value of a regular maintenance cycle tailored to individual business needs, which includes essential copier maintenance tasks and preventative maintenance work.
In this context, we will explore important preventative maintenance strategies and their practical applications to enhance the reliability of office copiers.
Routine Cleaning And Inspections
Your copiers will benefit from consistent cleaning and inspection to ensure all parts are in order. Essential tasks include:
- Cleaning the copier glass to prevent streaks on documents.
- Inspecting and cleaning document feeder rollers to ensure proper paper handling every time.
Preventing malfunctions by sweeping dust and debris from internal components is also crucial. Regularly emptying the waste toner reservoir in order to optimize print quality is another key task.
Utilizing quality toner and paper protects and optimizes copier quality. For example, all Canon models work best with the right supplies, significantly lowering the chance of experiencing a paper jam.
Component Replacement Schedules
Replacing consumables, such as toner cartridges, at scheduled intervals eliminates the inconvenience of sudden breakdowns. Companies keeping an eye on their usage each month, like 2,500 prints, can simply prepare for some wear.
Proactive replacement of rollers or fusers means no sudden workflow interruptions. This strategy helps maintain productivity and reduces downtime.
Firmware And Software Updates
Regularly updating copier firmware ensures that security and productivity are maximized. Neglecting updates can easily lead to vulnerabilities.
Automating updates makes keeping everything up to date a breeze. This not only enhances performance but also protects against potential security threats.
Steps For Effective Preventive Maintenance
Preventive maintenance for copiers is a great way to save on costly repairs and maximize the life of your office copier. By taking a proactive, structured approach through a copier maintenance contract, businesses can improve operations and reduce the impact that unplanned breakdowns have on a business, ensuring consistent equipment functioning.
- Use high-quality supplies to avoid equipment damage.
- Load paper correctly to minimize jams and misfeeds.
- Schedule regular cleanings to maintain optimal performance.
- Inspect for wear and tear to catch issues early.
- Update software regularly to ensure smooth operation.
1. Use High-Quality Supplies
The materials you feed through your copier, like toner and paper, affect its lifespan and functionality. High-quality materials help minimize the chances of operational failures, such as paper jams and lack of print quality. For instance, using premium-grade toner helps ensure the output is high quality and eliminates issues like smudging or fading.
Using durable paper prevents curling and static build-up. Using low-quality supplies can result in residue being left behind within the machine. This oily residue can lead to the slow but eventual destruction of key internal parts, like rollers and feed dogs.
Putting money into brands you trust protects your investment and leads to less service calls in the future. Businesses that make the quality of their supplies a priority usually find that they have greater productivity and less machine downtime.
2. Load Paper Correctly
Correctly loading paper is a simple but highly important preventive maintenance step to keep copiers running smoothly. Outdated equipment combined with misaligned paper can lead to constant jams, interrupting workflows.
To prevent this, always load paper stacks squarely and within the tray’s load limit indicators. Both overloading, which puts strain on feeding mechanisms, and underloading, which contributes to misfeeds, are concerns.
Using proper stock for each task—like heavier stock for presentations—keeps the copier in good working order. Accumulation of dust and debris in paper trays can affect performance. A weekly cleaning of trays avoids that problem.
3. Schedule Regular Cleanings
Over time, dust and debris can wreak havoc on a copier’s functionality, causing print imperfections and recurring mechanical errors. Regularly scheduled cleanings help protect main components such as glass surfaces, rollers, and vents.
A regular cleaning cycle, on a weekly or monthly basis, wears less and keeps small problems from becoming major repairs. For instance, keeping excess toner build-up off of print heads assures high-quality, crisp output.
With repeated use, preventive maintenance through regular cleaning reduces recurring downtime while ensuring a consistent, trustworthy performance.
4. Inspect For Wear And Tear
Regular inspections are the first step in preventing bigger issues down the line. Pay special attention to high-wear areas like rollers, belts, and print heads that are susceptible to wear and tear.
As an example, if rollers are worn, it can result in feeding issues and if belts are damaged it can cause uneven printing. Look for leaks or listen for other signs of malfunction like grinding or knocking sounds or overheating that indicate a failure is on the horizon.
By replacing worn parts before they fail, you’re eliminating the need for expensive repairs and maintaining a smooth operating condition.
5. Update Software Regularly
Running outdated software is not only detrimental to performance, but a serious security threat. Consistent updates fix bugs, improve functionality, and safeguard the platform from vulnerabilities.
For instance, firmware upgrades can improve energy efficiency and provide support for newer operating systems. Setting reminders for software checks ensures updates are never overlooked, keeping your copier running at its best and safeguarding sensitive business data.
Signs You Need Professional Maintenance Help
Despite diligent maintenance, copiers may still encounter problems that indicate it’s time to call in a professional. Understanding when to take action is key to preventing expensive maintenance repairs or disruptions to everyday business operations.
Read on as we dive into some of the telltale signs that it’s time to call in the professionals.
Persistent Hardware Malfunctions
Recurring hardware failures frequently indicate deeper issues that should be addressed as soon as possible. Machines that vibrate unnecessarily or don’t work on a regular basis may be signs of components that are getting old and worn out.
For example, dirty components might lead to jams or equipment failures, shutting down your operation. By taking care of these signs ahead of time, you can prevent problems from escalating into something that may cause complete equipment breakdown.
Maintaining a log of these errors will help any technician you may need to call in to diagnose the root cause and save you both time and money. By staying ahead of equipment issues, companies practicing proactive maintenance can increase equipment uptime by as much as 85%, creating a more efficient operation.
Frequent Error Messages
Error messages such as “paper jam” or “low toner” that persist despite troubleshooting often suggest deeper mechanical or software-related problems. Constant system crashes and pressing buttons leads to an inability to work and could be due to clashes from an update of the software.
Looking into repeating indicators and talking with the pros will make sure these problems don’t get out of hand. Experienced technicians quickly diagnose the root causes, getting you back in business with greater efficiency.
Businesses that invest in regular maintenance enjoy cost savings of 25–30%, proving that it’s worth reaching out for professional help before things go too far.
Declining Print Quality Despite Efforts
If print quality continues to degrade after you’ve cleaned or replaced consumables, it’s likely internal wear and/or alignment issues. Typical indicators are streaked or faded printing, which will compromise the high-quality presentation of your materials.
Expert maintenance evaluations can fix and prevent these issues, getting your system humming again. Performing treatment as soon as possible avoids more serious damage, especially when performance is still getting worse.
Consistent maintenance by professionals helps provide consistent results while lengthening the lifespan of your equipment.
Unusual Noises Or Overheating
Strange sounds, like grinding or clicking, are a sure sign that you have some loose or damaged parts. Overheating is another concern; overworking your machine is dangerous as it places a heavy load on the internal components, which can result in lasting damage.
It’s crucial to keep a lookout for these signs, as they can worsen over time if left untreated. Too much heat can also be due to a clogged ventilation or overuse, both of which need professional attention.
Only professional maintenance help can resolve these concerns completely, allowing you, your employees, and your patrons to enjoy a copier that functions safely and properly.
Choosing The Right Maintenance Service
Choosing the best copier maintenance contract for your copier service provider is another high-stakes choice with long-lasting effects on productivity and cost savings. A properly maintained copier decreases downtime, lessens distractions, and avoids costly repairs. Pay special attention to the length of contract terms, technician experience, and customer reviews. By taking these steps, you can ensure that your business gets the most value possible.
Evaluate Service Contracts
A detailed full-service maintenance contract should clearly spell out responsibilities and service guarantees. Ask about their response times and if they cover parts and labor and service in emergency breakdown situations. For equipment that’s used heavily, contracts that include regular weekly or monthly maintenance checks can be a wiser investment.
Review multiple contracts side-by-side to find a solution that best fits the organization’s operational needs, with terms that are easy to understand and operate.
Check Technician Qualifications
Trustworthy technicians have the kind of experience that gets you the right diagnostics and repair the first time around. Inquire about their certifications, any specialized training, and their experience working on your specific copier model.
Legitimate providers invest heavily in continuing education, ensuring their technicians have the most relevant skills to tackle even the most complex problems quickly and effectively.
Look For Customer Reviews
Customer reviews provide an unfiltered look into the quality of service you can expect. Customer reviews regarding response times, reliability, and problem resolution are great indicators for a provider’s consistency.
Read positive and negative reviews to get a sense of what to expect in advance of making a decision.
Compare Costs And Benefits
Consider service costs in relation to potential long-term savings. Playing catch-up with quality maintenance leads to costly, major failures – a reoccurring theme when repair vs. Maintenance discussions arise.
For example, businesses that have implemented predictive maintenance have seen cost savings of up to 25% over their reactive counterparts.
In-House Maintenance Tips For Businesses
Proper in-house copier maintenance, including a reliable copier maintenance contract, helps businesses avoid costly repair bills and lost productivity. With the right preventative maintenance practices in place, organizations can get the most out of their equipment, experience fewer disruptions, and save money. Below are high-level actionable tips and in-depth advice for keeping copiers in-house.
Train Staff On Basic Maintenance
Educating your employees on basic maintenance and copier maintenance routines pays off in spades. Employees who have a firm understanding can address minor inconveniences, like paper jams or replacing toner. This proactive approach catches small issues before they become major repairs.
For example, teaching staff how to properly clean scanner glass helps provide consistently clear prints and scans. Businesses should schedule regular training sessions, offering a manual or video for easy access. This helps cut back on reliance on outside technicians and helps maintain a seamless operation.
Create A Maintenance Schedule
Regular maintenance check-ups are the best way to ensure your copier is running smoothly. A comprehensive plan involves regular cleaning, inspection, and maintenance to make sure everything looks great.
For instance, creating a schedule of monthly reminders to dust any internal components removes dust accumulation that could hinder performance. High-use copiers need to be checked more often to make sure priority equipment is performing at its peak.
Making room in the schedule for inspections allows for more meaningful maintenance. No one wants to do a rushed or incomplete job.
Keep Spare Components On Hand
Keeping an inventory of critical components, such as rollers or fuser units, will allow for swifter repairs, minimizing costly downtime. Businesses can learn which parts tend to fail sooner depending on copier models and how they’re used.
For instance, keeping extra paper trays on hand avoids breakdowns during busy periods. Smart proactive stocking of parts goes a long way to showing that you’re ready and helps ensure seamless maintenance.
Monitor Copier Performance Regularly
Tracking copier performance assists in identifying bigger issues at hand before they arise. Whether it’s monitoring print volume metrics or error code reporting, these predictive maintenance metrics offer great insights into wear patterns.
For example, repeated paper jams may be a sign that your rollers have worn down and need to be replaced. Businesses can track logs to determine usage trends and plan preventive maintenance checks.
This comprehensive, proactive approach makes better use of public resources and helps prevent expensive, premature failures.
Benefits Of Preventive Copier Maintenance
Preventive copier maintenance is a proactive strategy that provides tangible benefits to organizations. With these benefits in mind, by embracing preventive copier maintenance, your organization can save copious amounts of money, achieve a more productive workplace, and establish a more reputable brand.
Here’s a closer look at how these benefits unfold:
Saves Money On Repairs
Preventive maintenance reduces overall repair costs by catching issues before they worsen, making it a crucial part of any copier maintenance contract. For example, identifying small wear before it leads to a complete machine failure or costly copier repair just makes good business sense. Consistent maintenance tasks help to extend the lifespan of the copier, eliminating costly replacement purchases and ensuring reliable equipment functioning.
Companies that make the switch to proactive care see a significant drop in costs due to unscheduled downtime, which can escalate to upwards of $5,600 per minute. This shift towards viewing maintenance as an investment, rather than an expense, is a financial no-brainer when weighed against emergency maintenance that disrupts productivity.
Regular preventative maintenance programs can save businesses money by reducing reliance on reactive maintenance, which can account for up to 40% of operational costs, allowing for a more confident monthly budget.
Boosts Workplace Productivity
Well-maintained copiers promote smooth workflows, having a direct impact on productivity. When equipment runs smoothly, it reduces rework, and employees can submit projects on time without scrambling at the last minute. Preventive maintenance lowers downtime by as much as 85%, so you can stay focused on business.
For instance, regular toner checks and software updates stop breakdowns that drag out work. Businesses that make maintenance a priority foster an atmosphere where tools are dependable, allowing teams to concentrate on what matters most.
Well-functioning equipment leads to fewer stops, which equals more productivity and better everyday operations.
Enhances Customer Satisfaction
Dependable copiers make for a dependable print quality, that’s extremely important for client-facing documents such as contracts or presentations. Your customers appreciate working with companies who provide consistent, reliable output, and having high-performing equipment goes a long way in building this confidence.
Preventive maintenance expands brand image into the realm of consistency in operations. When organizations put money into maintenance, they send a strong message that they value quality—improving their overall reputation.
By developing a strong alignment to customer expectations, companies can raise satisfaction scores, delighting customers and increasing both profitability and loyalty over time.
Supports Sustainability Goals
Keeping your equipment healthy with preventive maintenance is a green step. Preventing copier turnover helps reduce electronic waste, which furthers sustainability efforts by many organizations today.
Regular routine checks help maximize energy efficiency and minimize operational costs and environmental footprint. For instance, when internal components are cleaned regularly, the machine doesn’t spend as much energy trying to work through a jam.
Businesses that implement sustainable maintenance practices prove that they care, building their brand with eco-friendly consumers. This method is more eco-friendly and makes companies more attractive to the new generation of corporate leaders.
Challenges In Maintaining Copiers
Though office copiers are crucial to daily operation, ensuring their reliable equipment functioning becomes a hurdle that’s hard to predict. From technical blunders to poor equipment maintenance, the challenges can throw a wrench in the workflow and lead to large repair bills. Taking a proactive approach through preventative maintenance programs is the best way to ensure optimal efficiency and prolong equipment life.
Lack Of Technical Expertise
Most companies find it hard to stay on top of copier maintenance because of a lack of technical expertise. Without the right training, staff can easily mismanage even the most basic tasks, like cleaning the machine’s internal components or safely unclogging a paper jam. This exacerbates small fixable issues into big maintenance failures.
For instance, failing to clear paper dust regularly—a mostly invisible but easily identifiable source of trash—can jam mechanics, resulting in costly and frequent malfunctions. Whether through investing in staff training or consulting professional technicians, this bridges these gaps.
Expert technical support means accurate and effective troubleshooting, minimizing downtime and maintenance mistakes. This smart preventive approach can increase copier uptime while reducing future costs.
Ignoring Maintenance Schedules
Neglecting routine copier care leads to expensive consequences. Dust buildup, smudged copier glass from things like Wite-Out, or not allowing enough warm-up time after the weekend can put pressure on internal components.
In the long run, this disregard results in costly repairs or replacements. Sticking to a routine maintenance schedule that includes cleaning the machine and checking trays to ensure the paper is aligned correctly will help prevent these issues.
This consistency is key to keeping operational efficiency high and making sure machines are running with no hiccups.
Using Poor-Quality Supplies
Inexpensive toner and paper can be deceptive — they’re often the best way to destroy copiers. Poor quality consumables, such as substandard paper that tends to shed paper dust, can ruin rollers and sensors.
Just like with paper, low-quality toner can result in splotchy prints or even clogged moving parts. In order to protect machinery and keep operations running efficiently, businesses should invest in high-quality supplies.
High-quality materials or supplies mean less wear and tear, which leads to a longer lifespan for the copier and increased productivity.
Conclusion
Taking these simple steps will save your business thousands in repairs and downtime. Preventive maintenance nips minor issues in the bud before they develop into costly repairs. Clean parts, well-lubricated gears, and real-time repairs keep your copiers up and running. You cut costs, reduce downtime, and increase your machine’s longevity.
Neglecting regular maintenance invites expensive malfunctions and aggravating holdups. A well-maintained copier helps you avoid downtime and keep your team productive. Second, it prevents replacing the machine prematurely.
Be proactive about maintenance. Call in the pros when appropriate. Educate your staff on day-to-day maintenance. Taking these preventive copier maintenance steps can save you thousands in costly repairs in the long run. Begin investing in copier maintenance now. It’s a strategic decision that shields your bottom line and ensures your company remains competitive.
Frequently Asked Questions
1. What Is Preventive Copier Maintenance?
Preventive copier maintenance is the practice of consistent care, maintenance, and examinations of your office copier. This proactive approach allows you to catch and resolve smaller problems, such as toner issues, before they escalate into expensive repair bills. By implementing regular equipment maintenance, you ensure your business runs smoothly and minimizes downtime.
2. How Does Preventive Copier Maintenance Save Money?
Preventive maintenance programs are essential as they prevent major breakdowns in office copiers. Even the most reliable machines will break down at some point, but regular equipment maintenance prolongs your copier’s lifespan and cuts replacement purchases over time, saving your business thousands in large repair bills.
3. What Are Common Copier Problems Prevented By Maintenance?
Preventive copier maintenance, including regular equipment maintenance and servicing, prevents common problems such as excessive paper jams, toner leaks, and overheating. By implementing preventative maintenance programs, you can identify these issues before they escalate, ensuring your copier functions optimally and saves money over time.
4. How Often Should You Perform Copier Maintenance?
Preventive copier maintenance is essential and should be done at least every 3–6 months, depending on the frequency of use. For high-volume copiers, regular equipment maintenance is crucial to avoid excessive wear and tear, ensuring consistent equipment functioning and optimal performance.
5. What Are The Benefits Of Preventive Copier Maintenance?
Preventive maintenance extends your office copier’s lifespan, reduces print downtime, and improves overall print quality. By implementing regular equipment maintenance, you can lower long-term repair costs and avoid major operational disruptions, ensuring your copier performs when you need it most.
6. What Are Signs Your Copier Needs Professional Maintenance?
If you are experiencing constant paper jams, slow printing, or low-quality printouts such as faded prints and blotchy prints, you should call in a copier maintenance service technician for preventative maintenance. Ignoring these symptoms can lead to excessive repair bills and equipment downtime.
7. How Do You Choose A Reliable Copier Maintenance Service?
Find out how long they’ve been in business, read customer experiences, and inquire about their copier maintenance contract. Your trusted service provider should have transparent pricing, fast response times, and knowledge of your unique copier model’s maintenance needs, including regular equipment maintenance.
Transform Your Office With The Best High-Volume Copiers In Concord, California!
Are you searching for a reliable high-volume copier near Concord, California? Look no further! At Office Machine Specialists, we’ve been the go-to experts in servicing and selling top-notch office equipment since 1995. As a trusted family-run business, we’re committed to providing you with the best equipment options and exceptional after-sales service.
With decades of experience, choosing the right high-volume copier can be overwhelming. That’s where we come in. Our knowledgeable team will ask the right questions, understand your unique requirements, and guide you toward making smart decisions for your business. Whether you’re looking for a new machine lease or a purchase, we’ve got you covered.
We’ve witnessed the evolution of copiers from the pre-internet era to the cutting-edge digital workflow environment. Our expertise spans efficient high-volume printing, seamless scanning, advanced account control, and fleet management. Our extensive experience with all the major brands makes us the invaluable resource your organization needs.
Don’t settle for anything less than the best. Contact Office Machine Specialists today for all your high-volume copier needs. Let us help you streamline your office operations and increase your productivity!