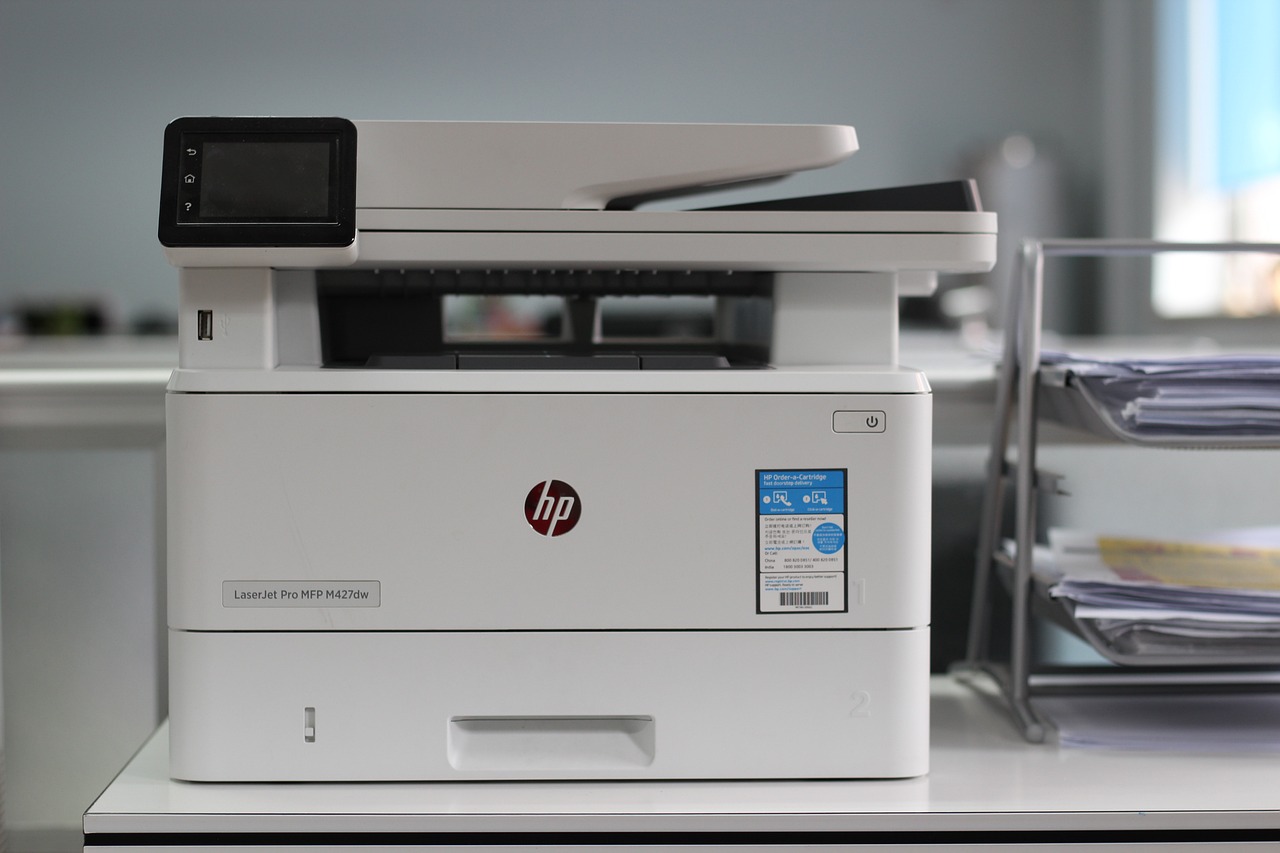
Key Takeaways
- Cheap copiers are more prone to jams because they cut corners when it comes to design and engineering, leaving out the precision and durability found in premium models. Shifting investments to better-engineered equipment can go a long way toward reducing unnecessary operational disruptions.
- Low-quality parts and inferior materials used in cheap copiers often result in breakdowns and shortened life expectancy. By focusing on high-quality materials, one can be assured of a more consistent, reliable output.
- The lack of ease of maintenance in low-end copiers does not allow for the simple upkeep of easy paper jam fixes. Choose models with easy-to-change maintenance items to improve ease of use and limit machine downtime.
- Appropriate paper handling and storage, as well as frequent monitoring, are necessary to prevent jams. Select the best paper quality with the correct weight and grain. To ensure your copier remains in pristine condition, store it in a cool, dry place.
- Frequent cleaning and preventative, scheduled maintenance are among the most important factors impacting copier performance. Create regular maintenance schedules and use certified professionals to stop never-ending mechanical issues in their tracks.
- Switching to a premium copier is just common sense over the long term. While the initial investment may be higher, premium models offer better performance, fewer jams, and lower operational costs over time.
Why do cheap copiers tend to jam more frequently than premium models? The answer lies in the differences in build quality, component durability, and design precision. In this post, we’ll explore how lower-cost copiers often rely on inexpensive materials, simpler mechanisms, and minimal paper-handling features—factors that contribute to frequent misfeeds and paper jams. These entry-level machines typically lack advanced sensors and are not built to handle high volumes or mixed media, making them less reliable in demanding environments.
Premium copiers, on the other hand, are engineered with superior components, tighter manufacturing tolerances, and intelligent features that ensure smoother performance and greater durability. As a result, they’re better suited for consistent, long-term use with fewer interruptions. Understanding these key distinctions will help you make more informed decisions when selecting equipment that meets your needs and reduces downtime caused by malfunctions.
Why Cheap Copiers Jam More Often
Ongoing paper jams in low-cost office copiers arise from a few intertwined causes. These printer problems are connected to the design, parts, and user behavior of the machines themselves. Without the same degree of precision and durability found in modern printers, these machines are prone to disruptions during high-volume printing periods.
1. Inferior Design And Engineering
Budget copiers generally use more basic designs to save money, but lose out on efficiency. Critical areas, like the paper path, don’t have the same smooth tolerances that would be necessary to avoid frequent jams.
Faulty engineering can lead to inefficient feeding mechanisms, which raises the risk of paper not aligning properly. Ultimately, over the long run, this design results in a miserable user experience, especially in work office settings where they need consistent performance.
2. Low-Quality Components Explained
Cheap copiers use delicate components such as plastic rollers and cheapo sensors. When you add the stress of high pressure and speed, these components wear out quickly, creating mechanical failures.
They can’t even pretend to keep consistent print quality, because the misaligned rollers lead to inconsistent feed rates due to varying feed rates. Over time, these cheap, inferior materials continually cause jams and require cumbersome, frequent replacements.
3. Substandard Materials And Manufacturing
This included the use of thinner plastics and less durable metals to cut costs, which makes cheap copiers much less reliable. Manufacturing processes for these complex machines typically have less stringent quality control, letting things like badly machined parts through the cracks.
These deficiencies inherently lead to an increased rate of jams and reduced longevity.
4. Precision Engineering And Tolerances
High-end copiers enjoy the advantages of higher tolerances, producing a machine that works well even when pushed to its limits. High-precision engineering eliminates <1mm spaces between moving components, removing the chances of misalignment.
This level of craftsmanship delivers a workhorse of a machine that you can depend on to perform flawlessly through years of heavy use.
Common Causes Of Paper Jams
Copiers rely heavily on fine-tuned machinery where paper is mixed with toner, electrostatic charges, heat, etc. Believe it or not, one of the top culprits is loading paper incorrectly. If the paper is not properly aligned or exceeds the tray’s paper capacity, it creates a hindrance in the feeder path.
This type of resistance usually results in annoying paper jams. Offices with high jam volumes—12 or more jams per month—usually know this is an ongoing issue. Frequent maintenance checks can identify if your rollers or other worn components are contributing to these problems.
Automated maintenance alerts are especially helpful in pinpointing these needs sooner, reducing overall disruptions.
The paper you’re using makes a huge difference, too. When low-quality paper—or paper that hasn’t been stored properly—comes into contact with moisture, it’s easily damaged. This leads to sticking or curling, which throws off the entire feeding mechanism.
Investing in high-quality paper with the right paper weight and finish helps minimize these risks considerably. Things like heavy cardstock and labels can be a challenge for some copiers, adding even more pressure to an already complex operation.
Toner quality is another big cause of jams. Lower quality toners, more common in rented machines, can create varying effects, resulting in dust settling on the interior of the copier. This hydraulic effect disrupts the even flow of paper across the machine, leaving you with the paper jams you dread.
Quality rental suppliers who keep their equipment in good repair and utilize quality consumables can make these issues less likely.
User errors due to things like outdated software or drivers add to that. Inaccurate instructions from malfunctioning firmware can confuse the printer and throw off the entire paper feed system.
Updating your drivers and firmware on a regular basis helps to make sure that your machine is operating at its peak performance and reduces the frustration for users.
Effects Of Frequent Paper Jams
Frequent paper jams in office copiers affect more than just the current printing task. These common printer problems erode productivity, raise the cost of operations, deteriorate morale, and lower the overall printer performance. Such issues are most apparent in mission-critical environments where downtime is not an option.
Impact On Productivity
Frequent paper jams are an operational productivity destroyer, due to the disruption of workflows that slows down office productivity. Each incident takes time to find the jammed paper, remove the jam, and reset the process.
In high-use settings like schools and corporate offices, 20 or more jams a month are common. In sum, these interruptions serve to burn up so many hours of invaluable time.
For instance, consider the case of a team working on time-sensitive reports. A jam in the middle of an important print run holds up these reports and the next round of work that’s waiting on their arrival. The ripple effect can dramatically decrease team productivity, making employees have to reschedule and rush work to meet due dates.
Increased Operational Costs
Jams frequently have invisible costs associated with them. In addition to the obvious, such as wasted paper and toner, constant jams result in increased maintenance costs.
Technicians will sometimes have to fix or replace parts, particularly with older machines that tend to age and wear out. That downtime is a big financial pressure too, as employees sit around doing nothing or get completely reallocated.
When you add all these costs up over time, it really adds up. Replacing these worn rollers on a five-year-old copier can be hundreds of dollars per year. You may think you can upgrade the components and bring that up to the thousands!
Frustration And Morale
Incessant paper jams alienate your employees, leading to decreased morale. Frequent paper jams lead to annoyance and interruption.
Reliable equipment creates a positive atmosphere and increased productivity, emphasizing the importance of investing in a reliable copier.
Select The Right Paper For Copiers
What kind of paper you run through your copier has a huge effect on its performance and your printed output. High-quality copiers jam less often, in part because when you use the right paper, there’s less chance of a jam. Making the right paper choice reduces the frequency of jams while improving your print quality.
Best of all, it furthers your environmental objectives and demonstrates your commitment to professionalism in your practice.
Paper Weight And Texture
Paper weight is an important consideration when choosing paper for copiers. Lightweight paper, such as 16-pound paper, can crumple up easily when being fed. Heavier stock, such as 32lb paper, could cause roller damage if your copier isn’t designed to accommodate these weighty choices.
If you’re using a standard office copier, 20- to 24-pound paper is usually ideal. Width and depth of texture play a role too—if the paper is too textured, toner won’t distribute evenly, or the machine can catch and ultimately slip or misfeed.
Too heavy or too rough can ruin copier equipment and lead to replacements and repairs. This wear results in more frequent jams and a greater need for maintenance.
Paper Storage Best Practices
Keeping paper in a controlled environment helps maintain paper integrity and prevent problems from occurring. Store paper in a climate-controlled environment, as moisture or heat can make the paper curl or stick together.
Stacked paper needs to be aligned evenly to avoid feeding issues. Re-sealing opened reams can protect unused sheets from dust and warping. These practices are critical to ensuring consistent performance and print quality.
Avoid Using Damaged Paper
Damaged paper, like wrinkled or torn paper, jams the feeding mechanism and can lead to jams. Check for creases and tears.
Inspect all paper before placing it into the copier. Even the smallest flaws will lead to misfeeds or uneven printing, so you’ll want to use only perfect sheets.
Copier Maintenance: A Proactive Approach
Regular, proactive maintenance of copiers is the best way to ensure these office workhorses stay up and running and protecting productivity day in and day out. By treating problems before they become worse, you will avoid an early breakdown and ensure the copier continues to perform at its best.
Preventive maintenance cuts down on the price of constant fix-ups. Perhaps even more importantly, it prevents sudden malfunctions and paper jamming operations from damaging your output.
Regular Cleaning Procedures
As with most tech, cleanliness is a huge part of copier maintenance. Dust and debris can quickly build up on internal components, including rollers and sensors, causing misfeeds and error codes.
Exterior cleaning should consist of wiping down the exterior and clearing the paper path to remove any dust daily.
Weekly maintenance should include an inspection and cleaning of any rollers, since the dirt accumulation can lead to paper slipping or misfeeding. Keep paper in a stable, cool, dry environment. This helps avoid moisture-related problems such as warping and decreases the chance of jams.
Adjust paper guides gently to avoid misalignment, and overloaded settings can jam the feeding mechanism.
Scheduled Maintenance Tasks
By scheduling regular maintenance, you can halt the development of these long-term problems. Monthly maintenance checks should include replacing machine wearables, like rollers and feed tires, and checking the machine’s performance overall.
Weekly maintenance and inspections should address the quality, movement, and alignment of the paper before printing begins. Filling up paper trays, even if you don’t exceed capacity, puts undue stress on machine components, so don’t fill the paper trays to the limit.
Downtime can be avoided by having a structured maintenance schedule to keep your copier functioning correctly and efficiently.
Importance Of Trained Technicians
Trained technicians know the best ways to resolve issues that often go unaddressed with DIY fixes. They can troubleshoot and remedy root causes, such as failing sensors or misaligned parts, before these develop into jams.
Proper professional servicing will guarantee detailed inspections and accurate adjustments, protecting you from expensive afterward repairs and wasted time with unexpected downtime.
Long-Term Jam Prevention Strategies
Preventing copier jams starts with understanding common printer problems and implementing proper paper loading techniques to avoid future issues. Cheap office copiers often lack robust components, making them more prone to persistent paper jams. With consistent effort, you can enhance printer performance and improve efficiency over time.
Implement Preventative Measures
Preventing long jams starts with proactive inspections and maintenance. High-volume environments need regularly scheduled check-ups to detect when parts are wearing or blowing out. It is essential to generally make sure things are operating optimally.
Last but not least, rental providers such as Office Machine Specialists provide a professional maintenance plan, including regular updates of firmware and drivers. These changes address chronic jam-prone paper handling weaknesses and maximize performance.
Good paper management goes hand-in-hand with ensuring safety. When loading stacks of paper, make sure they are squarely aligned and not bowed to avoid jams. Don’t overload trays, as overloading can expose internal mechanisms to excessive force.
Just educating your users on these practices can go a long way toward reducing jam risk. By ensuring levels of toner remain stable, quality issues are avoided that are known to cause hardware failures.
Train Staff On Proper Usage
Well-trained staff are an important long-term strategy to avoid copier jams. Training sessions should be tailored to the specific needs of staff, covering issues like loading paper properly, understanding low toner warning signs, and resolving common issues.
For example, training employees on how to clear small jams while avoiding jamming the paper will help prevent additional wear. With employees losing at least 22 minutes each day to IT-related problems, training reduces downtime and increases productivity.
Upgrade To Higher Quality Copiers
Buying high-quality copiers can have long-lasting benefits. These new models get sharper all the time – for example, with automated alignment, decreasing paper feed failures.
While initial investments can be greater, the dependability of high-end copiers means reduced servicing costs and less downtime. Working with equipment rental providers gives you access to reliable equipment that’s specifically designed for your unique needs.
Evaluating Used Copier Quality
When buying a used copier, proper evaluation is essential to guarantee years of reliable operation and professional results. Copiers, particularly well-used ones, can wear out considerably, making it vital to discern their condition as much as possible. Without scrutiny, you risk acquiring a device prone to frequent malfunctions, such as printer jams. These issues are often linked to overlooked problems like improper paper loading techniques or overworked components.
Inspect Key Components
Critical components such as rollers, fusers, and the paper feed mechanism should be focused on when checking the copier. Rollers showing signs of wear or cracking will not pick up paper properly, causing frequent misfeeds or paper jams. Fusers, the components that heat and bond toner to the page, have a lifespan and can fail, resulting in diminished print quality.
Door latches and paper feed mechanisms, if misaligned, can lead to constant stopping and starting. Check for indications of overstress and review the maintenance reports for replaced parts.
Check Usage History
A copier’s usage history provides important information, such as its expected PPM (Pages Per Minute) capabilities as well as its workloads. Anything over 30,000 daily should raise a flag that the internal parts are likely heavily used. A copier rated for 216 gsm gets put through its paces the minute you run a heavier stock through it.
This new layer of pressure frequently causes jams. Inquire with sellers about the previous usage and look for devices that do not have a history of erratic or high-stress cycles.
Ask About Maintenance Records
Maintenance records offer a detailed history and maintenance plan for a copier’s care. Ensure regular maintenance operations such as cleaning and driver updates, as older software may lead to operational disruptions.
Check service history to make sure records are legitimate and all significant services have been completed.
Buying Tips For Used Copiers
Here’s how to avoid common pitfalls when shopping for a used office copier to save yourself money and headaches in the future. Considering specific printing needs, researching printer models, and negotiating effectively are key steps to ensure you invest in a copier that suits both your budget and your workspace.
Define Your Needs
Start by evaluating your printing habits and workload. For instance, small businesses that print mainly text documents may only need a machine with 600 x 600 DPI, while larger teams handling high-resolution graphics or color printing might require advanced features like higher DPI or IoT connectivity.
Assess factors like monthly printing volume and space availability. Compact models are ideal for smaller offices, while larger units with multifunction capabilities may suit busier workspaces.
Remember, aligning your copier’s features with your requirements ensures efficiency without overspending.
Research Available Models
It goes without saying, but research is key. Look for well-known brands such as Canon ImageRunner, Xerox, or Konica Minolta that are reputable, durable, and perform well.
Review technical aspects such as copy speed, paper input/output capacity, and connectivity options. After that, read reviews from verified buyers to get a better idea of long-term performance.
Take IoT-enabled models, for instance. These solutions can significantly enhance business processes by automating and optimizing workflows. Further, be on the lookout for newer models because technology changes quickly, providing more advanced features at comparable prices.
Negotiate The Price
Having a good understanding of the fair market price gives you leverage in negotiations. Build trust with sellers by asking specific questions regarding the copier’s service history and current usage levels.
Watch for deals such as year-end clearances or back-to-school sales, especially in markets such as Minneapolis-St. Paul. Beware of hidden defects.
Always visit the copier before completing the purchase to check for covert problems.
Conclusion
Overall, cheap copiers are more likely to jam due to inferior materials and no high-end features like those found in premium models. Cheap rollers and the cheapest sensors money can buy lead to more jams. This is doubly true when encountering a mixed paper weight environment or heavy usage. Having to clear frequent jams creates time-wasting distractions that destroy productivity and add anxiety. Selecting higher-quality paper, making time for routine upkeep, and committing to a high-quality copier can all help to minimize these issues. Used copiers are an excellent option when properly vetted, so review the condition and service history before making a purchase. A time-tested, better-quality copier allows more time to be saved, frustration to be reduced, and continued work to be accomplished uninterruptedly. If you’re looking for less frustration and more productivity, invest in premium quality and proper maintenance. Spend intelligently, and your copier will do much more heavy lifting for you!
Frequently Asked Questions
1. Why Do Cheap Copiers Jam More Often Than Premium Models?
To save money, cheap copiers often rely on inferior parts and technology that can’t properly manage paper, leading to persistent paper jams and printer problems. Premium models, designed for high-volume printing, are built with better engineering standards and features to avoid this common paper jam issue.
2. How Does Poor Paper Quality Cause Jams?
Low-quality paper may be less uniform, producing jagged surfaces or more dust that creates a nightmare for productive feeding. Well-made copier paper is smoother and causes less friction, guaranteeing all-around smoother action and lessening the chance of paper jams.
3. Does Regular Maintenance Reduce Paper Jams?
Well, obviously, regular printer maintenance is important to avoid any jams. Remove any dust buildup and clean the print rollers occasionally to help your office copier avoid jams. Inspect for excessive wear and tear to reduce downtime from frustrating printer problems.
4. Can Using The Wrong Paper Size Increase Jams?
You bet your boots. Using improperly sized paper can significantly increase the risk of printer jams, as it won’t fit correctly into your office copier’s feeding mechanism, leading to misfeeds and persistent paper jams. To maximize reliability, always use paper that meets the printer model’s specifications.
5. Is It Worth Investing In A Premium Copier To Avoid Jams?
True, premium quality copiers, like modern printers, are designed to be more reliable and durable, featuring enhancements that help minimize common paper jam issues. While the upfront cost is higher, they save time and money in the long run by reducing interruptions and printer maintenance needs.
6. What Are The Common Causes Of Copier Jams?
The most frequent reasons for printer jams include low-quality paper, improper paper loading, and the age of the rollers. Addressing these printer problems proactively can enhance print speed and prevent your home printer from experiencing consistent paper jam issues.
7. How Can I Evaluate The Quality Of A Used Copier Before Buying?
For used copiers, it’s essential to check for wear on rollers, paper tray, and service records. Ensure proper paper loading techniques by running it with various weights and sizes of paper to confirm it meets your printing needs. A well-maintained used copier will have consistent paper jam issues no more often than a premium new model.
Transform Your Office With The Best High-Volume Copiers In Concord, California!
Are you searching for a reliable high-volume copier near Concord, California? Look no further! At Office Machine Specialists, we’ve been the go-to experts in servicing and selling top-notch office equipment since 1995. As a trusted family-run business, we’re committed to providing you with the best equipment options and exceptional after-sales service.
With decades of experience, choosing the right high-volume copier can be overwhelming. That’s where we come in. Our knowledgeable team will ask the right questions, understand your unique requirements, and guide you toward making smart decisions for your business. Whether you’re looking for a new machine lease or a purchase, we’ve got you covered.
We’ve witnessed the evolution of copiers from the pre-Internet era to the cutting-edge digital workflow environment. Our expertise spans efficient high-volume printing, seamless scanning, advanced account control, and fleet management. Our extensive experience with all the major brands makes us an invaluable resource your organization needs.
Don’t settle for anything less than the best. Contact Office Machine Specialists today for all your high-volume copier needs. Let us help you streamline your office operations and increase your productivity!